5G,6G通信システムで求められる高周波に対応した微細配線形成技術のお話
- makoto-oshibe
- 2022年12月26日
- 読了時間: 5分
更新日:2023年7月28日
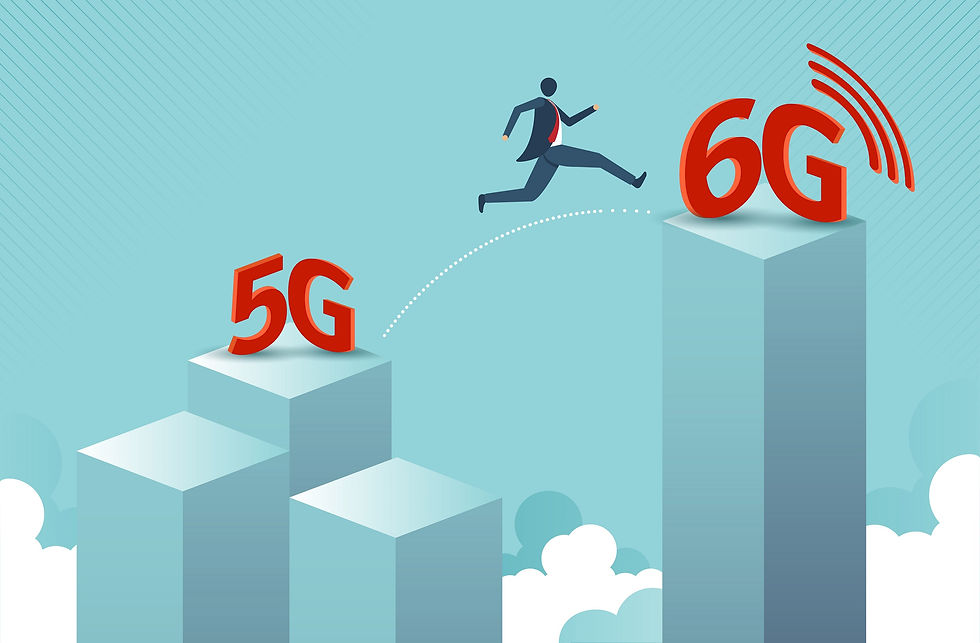
こんにちは、営業部のTZです。
現在、携帯ショップやニュース等で見かけることも当たり前となった「5G」という通信規格ですが、皆様はどのようなものかご存じでしょうか?
漠然と「4Gよりも通信速度が速くて、映画などの大容量データをあっという間にダウンロードできる」くらいのイメージをお持ちの方もいるかと思います。
5Gとは「第5世代移動通信システム」のことで、「高速大容量」「高信頼・低遅延通信」「多数同時接続」という3つの特徴があります。4Gが「スマートフォンのためのモバイルネットワーク技術」だとするならば、5Gは「社会を支えるモバイルネットワーク技術」といわれており、あらゆるものがインターネットに繋がるIoT時代を迎え、幅広いユースケースを想定されてます。
5Gでは、4Gに比べて高い周波数帯が使われていますが、周波数帯が高い電波は遠くに飛びにくいという性質を持つことが課題となっており、この課題を解決するための電子デバイスの開発に微細配線形成技術が必要とされています。
上記のような5G通信規格の普及、次世代の6G通信技術の開発に向けて、どのような表面処理技術が必要とされているかを本記事でご紹介させていただきます。
5G通信システムには周波数帯が2つあることをご存じですか?
5G通信規格には、実は2種類の周波数帯があることをご存知でしょうか?
それは「Sub6」と「ミリ波」と呼ばれている、2つの周波数帯で、
この2つのうち、期待されている大容量通信を実現できるのは「ミリ波」です。
一方で「Sub6」とは、6GHz未満の周波数帯を意味します。これまでの通信規格(4G)が700〜900MHz帯と1.5〜3.5G帯であるのに対して、Sub6の実際の周波数帯は3.5GHz帯と4.5GHz帯。4Gよりも少し高い周波数帯というイメージです。一方でミリ波は、桁が一つ多い、28GHz帯となっています。
高周波ほど、大容量のデータを短時間で送受信できますが、現在のところ、ミリ波はそれほど普及しておらず(カバーエリアが限られています)、ミリ波対応のスマホも機種がごく限られています。
その理由の一つとして、ミリ波のように高い周波数帯では、電波の伝わり方が異なり、高周波ほど、直進性が高くなり、減衰しやすく遠くまで届かないという性質があることが挙げられます。建物のような障害物だけでなく、木の葉や、雨の影響さえも受けてしまいます。
ミリ波通信において、スマホなど携帯端末機器から送受信するには、アンテナから近距離でかつ障害物に邪魔されないエリアであること、もしくは障害物を迂回するためのアンテナ機器の設置が必要となり、ミリ波通信が使えるエリアは、専用アンテナが設置された周囲のスポットに限られています。

高周波通信における配線回路の技術的な課題
現在、5Gとそのさらに先にある6G(100GHzを超えるテラヘルツ帯)の通信技術の実現に向けて様々な研究開発が盛んに行われています。このような高周波通信に対応した電子デバイスにおいては、配線回路における伝送損失(伝送ロス)をいかに減らすかが重要課題となっています。
10GHzを超えるような高周波帯になってくると、伝送損失が大きくなり、電気信号の減衰が顕著になってきます。この伝送損失は、「誘電損失」と「導体損失」からなり、回路に使われる絶縁材料、配線材料それぞれが持っている特性によって決まります。
伝送損失 = 誘電損失 + 導体損失
誘電損失は主に、回路基板材料の誘電特性(誘電正接と誘電率)に起因します。
プリント基板に使われるガラスエポキシ樹脂やポリイミド樹脂、半導体デバイスに使われるシリコンは、高周波特性の点においては伝送ロスが大きいため、代替材料の開発が盛んに行われています。
ガラエポ樹脂の代替材料として、変性ポリイミド、液晶ポリマー、テフロン(PTFE)などが挙げられます。また、シリコンウエハの代わりに誘電特性に優れるガラス基板を用いたり、シリコン上に高周波特性に優れた樹脂膜を塗布するなどの方法が挙げられます。
ガラス板にアンテナの配線を形成することで、ガラス窓自体を基地局化しようという動きがあるのは、上記のようにガラス材料が高周波特性に優れ、かつ景観を損なわずに低コストで設置できるなど、いくつものメリットがあるためです。
一方、導体損失においては、配線の電気抵抗や表面粗さが影響します。配線材料には銀(Ag)の次に電気抵抗が低く、かつ安価な銅(Cu)めっき配線が多く用いられています。結晶粒界が多いほど電気抵抗が高くなります。また、高周波になるほど、「表皮効果」により、配線の表面に電流が集中して流れるため、表面の凹凸が大きいほど導体損失が大きくなることから、高周波においては配線の表面の平滑性が求められます。
次なる課題は「配線と基板材料の密着性」
従来のプリント基板では、樹脂の表面をエッチングにより意図的に荒らして凹凸を形成することで得られる「アンカー効果」により密着力が保たれてきましたが、配線の微細化と、配線の表面の平滑性が求められるようになってきたことで、アンカー効果が期待できず、配線が剥がれやすくなるという課題が浮上してきました。
高周波電流が流れる微細配線においては、基板と配線の表面がツルツルであっても、高い密着性を実現しなければなりません。そのための方法として、従来の物理的な密着ではなく、化学的な結合を利用した表面処理技術が開発されています。
デバイス、材料、装置メーカーによる協業の重要性
生産プロセスの確立、採算性の評価と設備投資判断、量産化を短期間で確実に実行には、デバイスメーカー、材料メーカー、装置メーカー、受託加工メーカー等、それぞれが得意とする技術を持ち寄って、協業することが必要不可欠だと考えています。
弊社では、このような先端技術の開発動向を見据えて、めっきプロセスを中心とした独自のプロセス開発ならびに装置開発に取り組みながら、お客様との共同開発、評価を行っています。
関連記事として、下記2つの記事も公開しておりますので、是非ご覧ください。
「HPに「デモ・試作・受託加工サービス」のページを追加しました」
最後に
いかがでしたか?
5G,6G時代の電子デバイス用途の微細配線形成技術の開発に取り組まれている企業様からのお問合せをお待ちしています!
東設めっき技術に興味を持っていただいた方はこちらから。
↓
Comments